How Industries Gain from Using a Effective Chemical Defoamer
How Industries Gain from Using a Effective Chemical Defoamer
Blog Article
Comprehending Exactly How a Chemical Defoamer Works to Enhance Industrial Processes
Chemical defoamers play a crucial role in enhancing commercial processes by effectively minimizing foam-related obstacles. Their capacity to reduced surface area tension and interfere with bubble development translates into smoother operations and enhanced performance. The systems behind their action and the range of readily available formulations require a closer examination. Recognizing these aspects can disclose significant insights right into not just enhancing manufacturing but additionally accomplishing cost savings across numerous fields. What stays to be explored is just how these defoamers can be tailored to fulfill particular operational needs.
What Is a Chemical Defoamer?
A chemical defoamer is a material specifically formulated to lower or remove the formation of foam in various commercial processes. Frothing can hinder production efficiency, affecting the top quality and performance of products in industries such as food and beverage, pharmaceuticals, and wastewater treatment. Defoamers are critical in these applications, as excessive foam can bring about operational obstacles, such as overflow, lowered blending efficiency, and prevented warmth transfer.
These representatives generally contain a mix of surfactants, oils, and other additives that work to undercut the foam structure. They are created to swiftly move to the foam's surface, effectively damaging the surface area stress and permitting for the collapse of bubbles. The choice of an appropriate defoamer is essential, as various solutions may be customized for details procedures or sorts of foam (Chemical Defoamer). Factors such as compatibility with various other components, temperature security, and the designated application play a considerable role in the effectiveness of a defoamer.
Mechanisms of Defoaming Action
The systems of defoaming action involve complicated interactions in between the defoamer and the foam framework. At the core of this procedure is the decrease of surface area stress at the user interface of the fluid and gas stages. When a defoamer is presented to a lathering system, it migrates swiftly to the surface area of the foam bubbles, displacing the supporting representatives that contribute to foam stability. This displacement weakens the foam structure, bring about bubble coalescence.
As smaller bubbles combine right into larger ones, the overall security of the foam reduces. In addition, certain defoamers might include hydrophobic components that improve their capacity to undercut the foam by developing a barrier that inhibits bubble formation. This double activity-- surface area tension reduction and destabilization-- enables an extra reliable breakdown of foam.
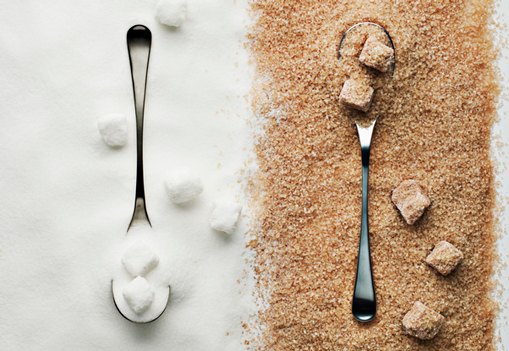
Additionally, the thickness and spreading attributes of the defoamer play essential functions in its efficiency. A well-formulated defoamer will certainly make certain rapid movement and ideal efficiency, reducing foam development throughout commercial procedures. By comprehending these systems, sectors can better select and use chemical defoamers to enhance operational efficiency and item top quality.
Types of Chemical Defoamers
Chemical defoamers can be categorized right into numerous types, each tailored to particular applications and foam obstacles. The key categories consist of silicone-based, non-silicone-based, and powder defoamers.
Silicone-based defoamers are very effective because of their ability to spread quickly across liquid surface areas. They provide superb foam suppression and stability, making them ideal for various commercial applications, including finishings and adhesives. Non-silicone-based defoamers, on the various other hand, typically rely upon organic substances like fats or esters. These are particularly favored in food and drink markets because of their low poisoning and regulatory conformity.
Powder defoamers consist of solid fragments that can be contributed to dry procedures or solutions. They are typically utilized in procedures where fluid defoamers may not work, providing a special option for specific applications, such as in the manufacturing of certain sorts of plastics or powders.
In addition, each kind of article source defoamer can be customized with numerous ingredients to improve effectiveness, such as emulsifiers or surfactants, enabling versatility in resolving different frothing situations across multiple markets.
Applications in Industrial Processes

In the food and beverage sector, defoamers are crucial throughout the production of juices, beers, and milk products, where too much foam can impede blending and purification procedures. By minimizing foam development, defoamers assist page maintain consistent item high quality and optimize handling times.
In pharmaceuticals, the presence of foam throughout the blending and solution of medications can impact dose accuracy and item security. Defoamers guarantee smooth operations, thus facilitating the manufacturing of high-grade drugs.
Wastewater treatment facilities also rely upon defoamers to manage lathering in oygenation storage tanks, which can otherwise reduce treatment effectiveness and make complex sludge handling. By properly handling foam, these chemicals boost the general efficiency of therapy processes and add to governing conformity.

Benefits of Utilizing Defoamers
While foam can provide significant challenges throughout various sectors, making use of defoamers uses countless benefits that boost functional effectiveness and product honesty. Defoamers efficiently minimize or get rid of foam formation, resulting in smoother production processes and enhanced item quality. This reduction in foam lessens disturbances during production, permitting for continual operation and enhanced throughput.
Furthermore, the application of defoamers can lead to cost financial savings by lowering the need for excess resources and power consumption connected with foam monitoring. By maximizing the production procedure, suppliers can achieve higher yields and reduced waste, ultimately boosting success.
Furthermore, defoamers add to much better devices performance. Foam build-up can cause blocking, overflow, and devices wear, causing costly downtime and maintenance. By avoiding these problems, defoamers prolong the life-span of equipment and minimize functional costs.
Conclusion

A chemical defoamer is a substance especially developed to eliminate the development or decrease of foam in different industrial procedures. When a defoamer is introduced to a frothing system, it migrates rapidly to the surface area of the foam bubbles, displacing the stabilizing representatives that contribute to foam security. A well-formulated defoamer will ensure quick movement and optimal performance, reducing foam formation throughout industrial processes. Defoamers properly eliminate or decrease foam formation, leading to smoother manufacturing processes and enhanced product high quality.In verdict, chemical defoamers play a crucial function in boosting commercial processes by successfully minimizing foam formation.
Report this page